When manufacturing plastic bottles, there are several different types of defects that will cause your quality department to scrap that particular bottle. If any of the following defects were to make it past your quality department and end up in the hands of your customer or their consumer, your relationship could be heavily impacted.
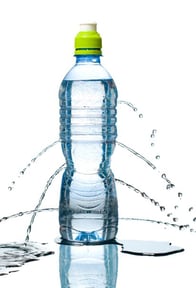
ALPS Inspection equipment and subsequent production processes can reject a bottle for any defects where air can escape during the leak test. Different machine options are available to effectively reject plastic bottle defects, based on your blow molding process and equipment.
The faster you can identify the cause of these issues, the more money your company can recoup from your production line. Resulting in a stronger customer relationship.
The following is a comprehensive listing of the various types of plastic bottle defects that can occur in your production line and blow molding process. ALPS Inspection manufactures testers for every type of defect. No matter what production process and raw plastic material you use, we have a leak tester for you.
Holes
Holes in plastic bottles can occur in various stages of the blow molding process. There are many causes of holes, however some of the most common causes are:
- Contamination in the plastic: Can occur anywhere in the container. The contamination does not stretch like plastic does, so the area around the contamination gets too thin, and a hole develops.
- Improper material distribution: Causes thin areas of material that are stretched so far that a hole develops.
- Mold wear or improper setup: If the two halves of the mold do not close properly, the plastic may be blown out through the gap and cause a hole (this is possible in any process). Or if the mold doesn’t pinch the parison properly to seal the top or bottom, a leak can develop at the top or bottom (this is an extrusion blow molding or EBM problem).
If you have a blow molding defect, we can help! Our Feasibility Test can help determine the root cause of your plastic bottle defect. Learn more now!
Laser Code Holes
A Laser Code Hole is a specific type of hole that can occur on any line using laser coding for the containers. These holes are caused by the laser burning through the plastic, which could be from a thin area, the power of the laser turned up too high, or the container not moving past the laser as fast as expected.
Gate Leaks
Gate Leaks are a specific type of hole that can occur during either the plastic bottle injection blow molding process (IBM), injection stretch blow molding process (ISBM), or 2-step PET blow molding process. These processes have an injection step that forms a gate in the preform. There are several possible causes for gate leaks in plastic bottles, including, but not limited to:
- Thin areas or holes in the gate during the injection step
- Improper heating of the preform when going into the blow mold step
- Bent or improperly adjusted stretch rods in the blow mold step
The turntable vacuum option of the ALPS NextGen Rotary leak tester, NGR, will draw more air out of the plastic bottle through the leak in the bottom so the leak test detects a smaller hole.
A hole in the sidewall leaks air at a rate based on the test pressure versus atmosphere. A hole in the base will have a greater pressure difference between the test pressure and the vacuum generated under the base. To be effective, the bottom of the container must seal to the turntable, so the full vacuum is applied to the gate area.
If there are channels in the container design that allow air from outside the container to be drawn to the vacuum hole the vacuum level at the gate area will be reduced.
Short Shots
A short shot is a defect that can occur on the IBM, ISBM, or the 2-step PET. These processes have an injection step that forms the finish in the preform.
During the injection step, the plastic flows to the end of the mold cavity to form a precise finish. If the plastic does not flow fully into the cavity, a low area, or notch in the seal surface will occur. In other words, the molten plastic injection is short and leaves the plastic bottle incomplete and deficient, hence the name “short shot.”
By using harder durometer seals on the probe and reducing the probe pressure, the notch or low area will appear as a leak. While a flat finish will seal against the probe.
Finish Trim Defects
Finish Trim Defects are specific plastic bottle defects that can occur in the EBM process. There is no trim operation in IBM, 1-step PET, or 2 Step PET.
These defects are usually caused by worn equipment or improper setup of trimmer. With a rotary trimmer, there can be “hangnails”, which are cuts in the seal surface. On a punch trimmer, the trimmed surface can be torn.
With either trimmer, the finish could be uneven when the customer has a requirement for it to be flat.
Like detecting short shots, all ALPS leak testers have a range of seal durometers. The durometers can control the probe pressure to make the finish trim defects appear as a leak.
Cocked or Tilted Necks
Cocked or Tilted Necks are plastic bottle defects that can occur in all processes. They are caused by uneven raw material distribution usually in the neck or shoulder. As a result, one side cools and contracts unevenly from the other.
This may also be a function of the bottle design. For example, on a container with a handle and offset neck, the material near the handle end will have thicker plastic and more structure than near the finish. As a result, the finish may tilt as the container cools. Additionally, this can also be caused by a PET preform being loaded into the blow mold improperly. Non-tilting probes with harder seals and reduced probe pressure will contact the high side of the finish but not the low side. This will prevent a full seal that appears as a leak.
Get your plastic bottle tested to determine the type of container defect and how to fix it.
Choked Necks
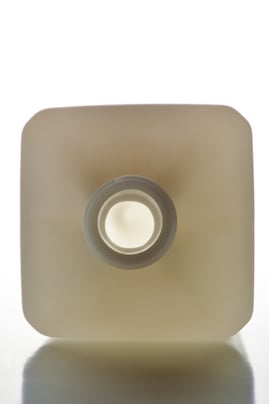
Choked Necks typically occur during the EBM process, when the neck is long with a small diameter. These plastic bottle defects are caused by the parison collapsing or wrinkling as the mold closes on it. The plastic either contacts the opposite side, and when the container is blown, the plastic stretches across the neck ID, or the wrinkle leaves a piece of plastic closing off one side of the neck ID, as the material does not get blown against the inside of the mold.
When the plastic bottle goes into the filler, the fill tube may get damaged by the material in the opening, or it may get caught in the neck, causing a jam.
Choked neck probes have a nose cone that is inserted into the container neck, and if there is a choked neck, it will not go all the way into the container to seal on the top of the finish (fixed choked neck probe), or compress a spring and trigger a switch (choke sensing probe).
The fixed choked neck probe is available on all ALPS machines, including the BottleStop Multi Head Leak Tester (designed for angle neck and choked-neck prone containers). The choke sensing probe is also available on the single head linear leak testers: RS, SX, and QuickCheck models.
In addition to the leak test, plastic bottle height inspection options are available, including:
Gross Height, Single Sensor (topload check)
- With a single reed switch sensor on the probe cylinder it can reject a bottle that is too tall, or too short (not both).
- This can also be used to verify the topload of the bottle. Topload is the force that the bottle neck/shoulder will support before collapsing. This is a gross test of topload, using the probe force from the cylinder. If the container collapses under the force, the sensor will be triggered as if the bottle is too short. This is only a gross measure of the container height and is subject to how accurate the user can set the position of the sensor on the cylinder.
- On a multi-head machine, there is also the question of how consistent the user can set the sensor position from one head to the next. Accuracy is also improved when the bottle is on a turntable (NGR) or on a stopped conveyor (SC Linear)
Gross Height, Dual Sensor
- With two reed switch sensors on the probe cylinder, this option can detect plastic bottles that are too tall or too short or verify the topload of the container.
- Like the single sensor, this is a gross measure and subject to how accurate the user can set the positions of the sensors, and the consistency of how the bottler is presented to the head.
This is available on ALPS single head leak testers SC, RS, and SX
Accu-Height Cylinder
- This is a cylinder with analog output of its position.
- Provides greater accuracy of the bottle height measurement
- The zero point and height tolerances are set through the HMI for easy, consistent setup.
- Limited to 1” stroke cylinder, so cannot be combined with longer choked neck probes, or angle neck applications.
This is available on ALPS single head leak testers (SC, RS, and SX-limited to 1” stroke cylinder).
Laser Height Detection
- This is a Keyence laser sensor mounted over conveyor at infeed (Speed Glider, FlexPitch) or exit starwheel (NGR).
- Provides greater accuracy of the plastic bottle height measurement.
- Special setup bottle used to zero the sensor, to the nominal container height.
- User sets tolerances in the sensor.
Can be used at speeds up to 400-600bpm, depending on the handling, and plastic bottle dimensions. A leak inspection system will greatly enhance your production line. Read our blog to discover what to look for when it comes to your unique production line and blow molding process.
ALPS Inspection has been testing empty plastic bottle defects for over 25 years. We have seen every type of bottle defect and have engineered solutions to detect and reject impacted containers. ALPS Inspection understands the business consequences of defective containers. We help you to identify and overcome issues before they reach the consumer with our Feasibility Testing services.
Contact us today to learn how we can benefit your production process.