Understanding Plastic Container Defects and Defect Feasibility Testing
The best way to maintain your company’s reputation and customer trust is to ensure every plastic container that leaves your manufacturing facility is of the highest quality. Even the smallest defect can produce negative outcomes, including poor or inconsistent product quality and brand reputation.
Understanding the most common types of plastic container defects is the first step to knowing you have the best leak testing system for your manufacturing needs. You should feel confident your leak tester will reject defects and, as applicable, provide the insight needed to help prevent future ones from happening.
ALPS Inspection offers dependable, pressure decay leak testing systems designed to catch even the smallest container defect in accordance with your specifications. What’s more, sending in faulty, rejected containers to our defect feasibility testing lab can help check machine performance and identify inefficient and faulty areas in your blow molding manufacturing process.
Have a plastic container defect sample? Ask our team about Defect Feasibility Testing today.
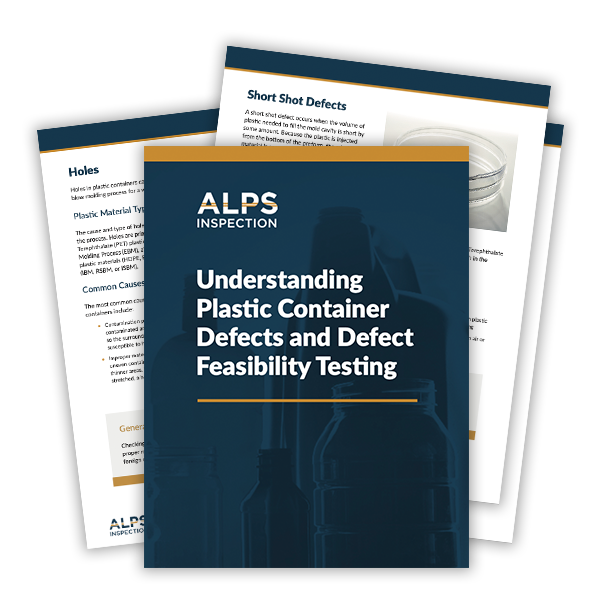
Understanding Plastic Container Defects and Defect Feasibility Testing
Maintain your company’s reputation by ensuring every plastic container that leaves your blow molding facility is of the highest quality. Download our guide to learn more about defects and how to prevent them.
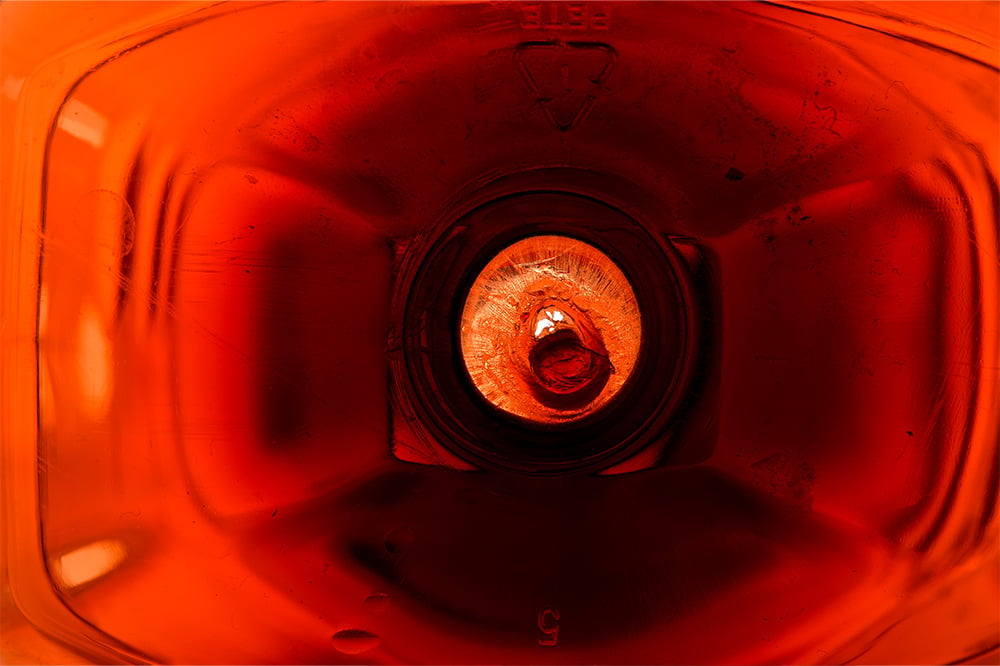
Types of Container Defects
Plastic Container Feasibility Testing
Through our Feasibility Testing services, we cover two primary customer needs when it comes to catching and identifying plastic container defects: testing machine capabilities and categorizing and determining the severity of a defect.
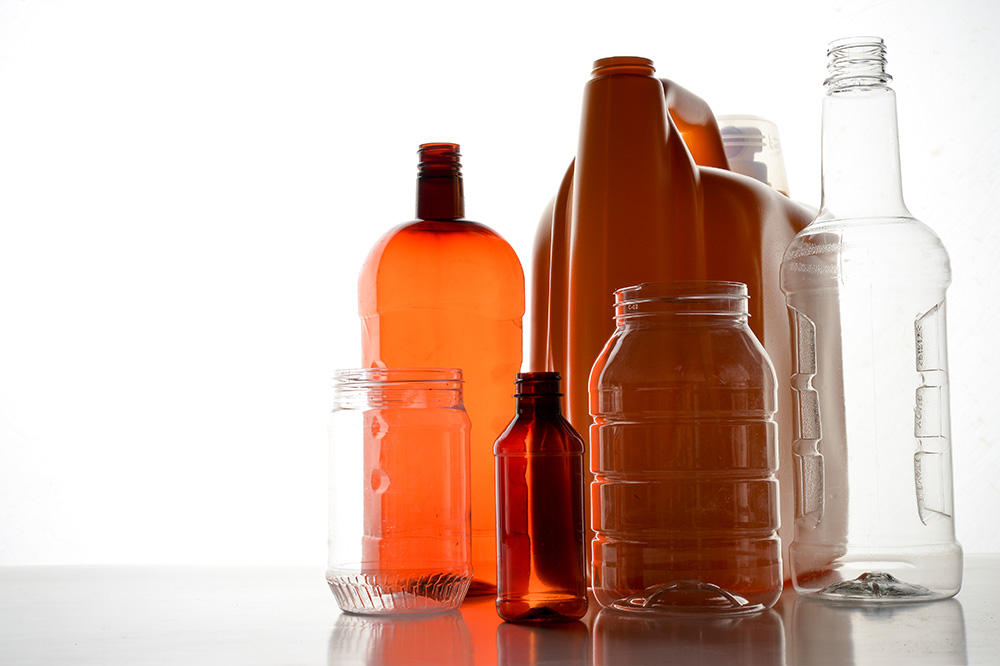
Feasibility Testing
Before investing in leak testing equipment, you want to make sure you choose the best system for your production line and product inventory. Feasibility Testing takes a good container sample from your production line and determines if a leak testing machine can test the type of container your company uses and whether it will reliably detect the hole size (or other leak source) you need to maintain the consistent and reliable performance of your manufacturing line.
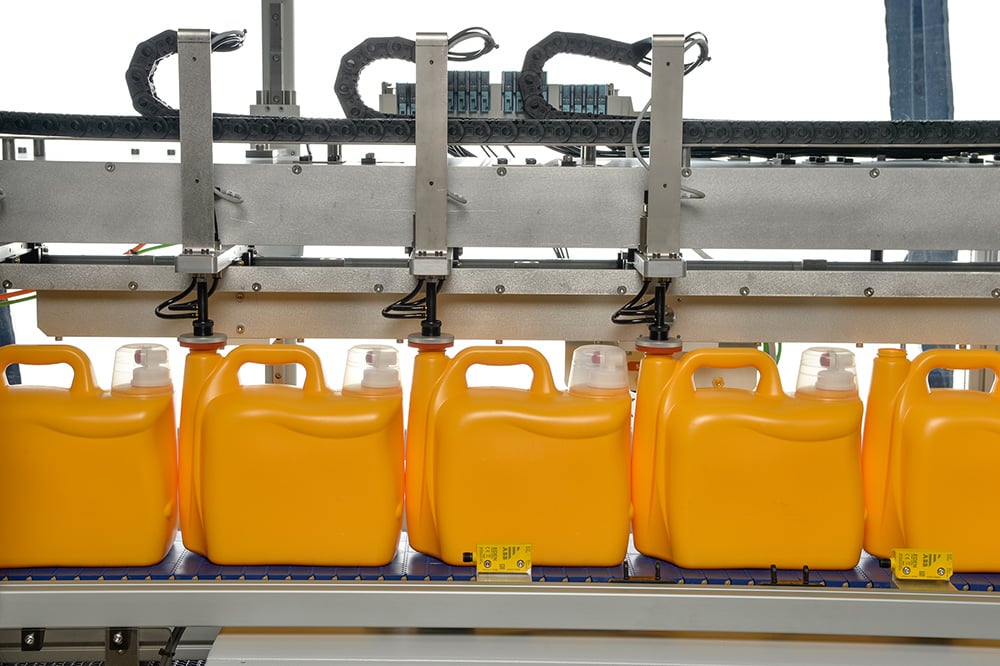
Defect Feasibility Testing
Defect Feasibility Testing takes a rejected container from your line and identifies the type of defect and hole size.
Many factors can cause a plastic container defect, including the material, container handling, machine setup, and component wear. Therefore, it can be challenging to pinpoint what may be causing the issue on your production line and how to fix it.
By sending your defective plastic container to our facility, you can gain valuable insights to troubleshoot issues on your production line. In addition, our experienced engineering team will assess the defective container and recommend potential adjustments to your leak detector or suggest alternative machines that will effectively reject products with this issue. This proactive approach helps prevent any defective items from reaching your customers' hands, ensuring the highest level of quality control.
Have a plastic container defect sample? Ask our team about Defect Feasibility Testing today.
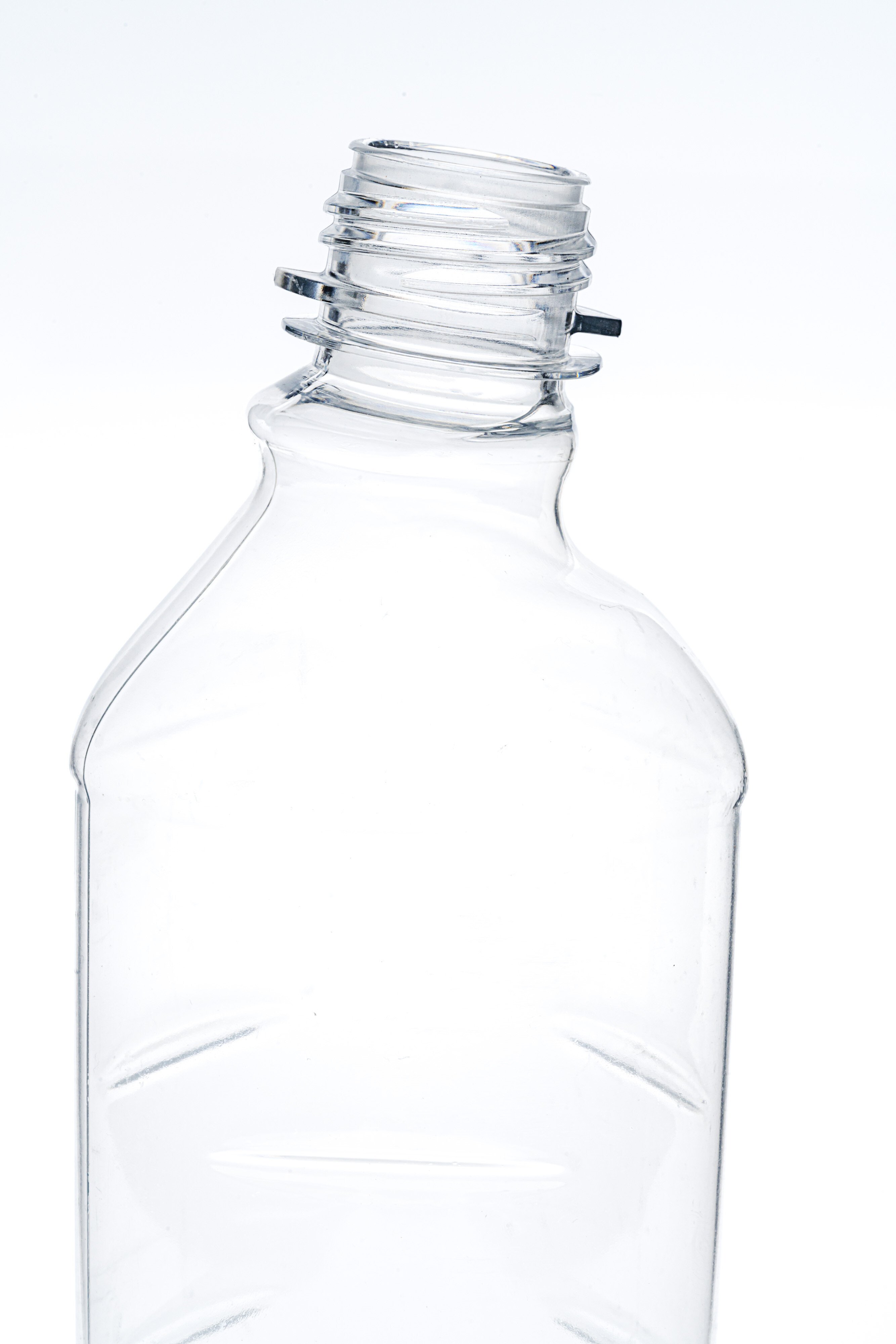