Leak Testing PCR Containers
With more focus on sustainability, Post-Consumer Recycled (PCR) material is on the rise and expected to become the industry standard. While utilizing PCR material is environmentally friendly as it reduces the amount of single-use plastics in the market, it also has the potential to add more risk to the durability and integrity of your empty container packaging.
ALPS Inspection’s leak testing machines will be more valuable than ever to mitigate these risks. We can help you protect your product and customer by ensuring every PCR container that leaves your facility is defect-free and holds up to your highest quality standards.
Download Our Guide on Leak Testing PCR Plastic Containers
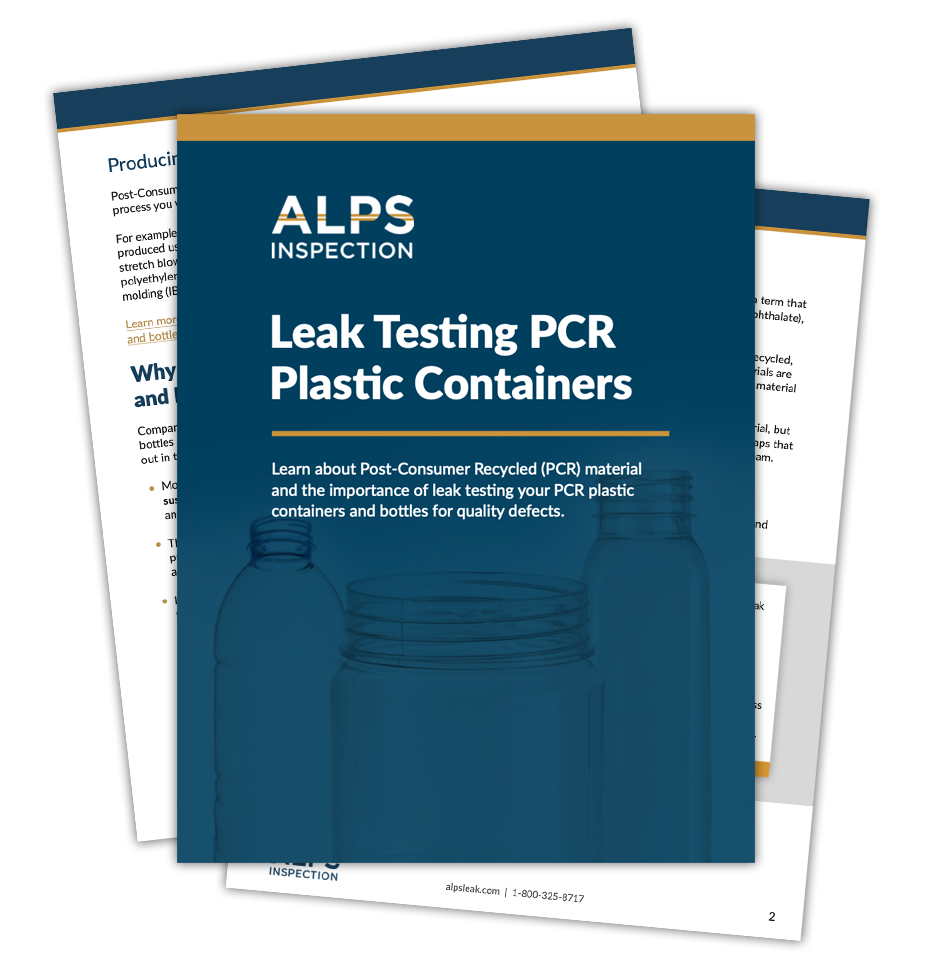
Download the PCR Plastic Container Guide
What is Post-Consumer Recycled Plastic?
Post-Consumer Recycled Plastic (PCR), also called Post-Consumer Resin, is an umbrella term that encompasses various recycled plastics sourced from rPET (Recycled Polyethylene Terephthalate), rPP (Recycled Polypropylene Plastic) and rHDPE (Recycled High-Density Polythene).
Post-Consumer Recycled Plastic is made from items customers have already used and recycled, including water bottles, beverage bottles, and packaging materials. These recycled materials are collected and sent to facilities, where they are sorted, ground, and/or melted down. The material can then be molded and used again in new packaging forms.
Some manufacturers may say their packaging product has a percentage of recycled material, but this does not mean it's PCR plastic. This type of recycled material refers to the excess scraps that have been collected from the manufacturing process and sent back into the recycling stream.
How is PCR Plastic Created?
The two types of recycling processes used to create PCR plastic are mechanical recycling and chemical recycling.
- Mechanical recycling is a step-by-step process. The recycled plastic item is collected, sorted at a facility by type and color, washed, and then melted and reprocessed into pellets. These pellets are then transformed into raw materials for new plastics. This process does not break down the plastic’s molecular structure, meaning there’s a chance contamination may impact the finished product.
- Chemical recycling uses chemicals to break plastic down to the molecular level. This plastic is then processed the same way you would use those chemicals to create virgin plastic. Chemical recycling doesn’t require thorough sorting and can recycle most plastics together. Contamination and impurities are less frequent with this process when compared to mechanical recycling, resulting in a more durable finished product.
The type of recycling process can greatly influence the strength and integrity of PCR packaging products and determine how quickly you need to add leak inspection equipment to protect your brand, products and customers.
Ensure quality before full production. Test your PCR container design with the BenchPlus Manual Leak Testing system. Learn more!
Producing PCR Containers and Bottles
Post-Consumer Recycled containers and bottles are produced using the same manufacturing process you would use to make a container from its virgin plastic form.
For example, similar to PET containers, rPET plastic containers and bottles are most commonly produced using the 1-step stretch blow-molding (ISBM) process or the two-step, high-speed stretch blow molding (RSBM) process. The same goes for rHDPE (recycled high-density polyethylene) containers, which are typically produced using an extrusion or injection blow molding (IBM) process.
Learn more about the blow molding processes used to create empty plastic containers and bottles.
Why Are More Companies Using PCR Containers and Bottles?
Companies are voluntarily switching to PCR containers and bottles to decrease their environmental footprint and stand out in today’s market.
- More and more consumers are considering sustainability a primary concern in product selection and brand loyalty.
- This shift in consumer environmental consciousness has prompted many industry leaders like Kraft Heinz, Mars, and Unilever to use PCR bottles.
- In addition, new laws have also opened industry eyes to the need for PCR containers and bottles. A recent California law requires plastic bottles to contain at least 25% of post-consumer plastic by 2025 and 50% by 2030. Washington state also recently enacted a similar law, and this trend will only get stronger as other states follow suit.
Learn how container designs are changing in the packaging industry and how you can ensure consistent quality.
Advantages of Using PCR Content for Your Containers and Bottles
Environmental advantages of using PCR content include:
- PCR offers a significantly lower carbon footprint compared to virgin materials.
- Creating less waste that will eventually fill landfills and waterways.
- Less petroleum used in the PCR creation process compared to virgin plastic.
- Raise awareness of recycling while promoting the circular economy.
Business advantages of using PCR content include:
- Increases brand reputation and image.
- Great marketing opportunity to appeal to the rising number of eco-friendly consumers.
- Depending on oil prices, PCR can be more cost-effective than virgin plastic.
Disadvantages of Using PCR Content
While using PCR content for your packaging can be great for both the environment and may set your business as a leader in the sustainable packaging market, it comes with some challenges.
Foreign materials, such as metal, ceramics, and debris, get into plastic every time you recycle. This material gets melted into the mold during the blow molding process, causing contamination and bottle or packaging weakness.
Contamination can damage the integrity of the finished PCR product, resulting in defects like pinholes and thin spots that may lead to leaks.
Learn more about what causes bottle defects and how to prevent them.
Other disadvantages of using PCR content include:
- The required heating process can alter the color or clarity of the bottle. The higher the concentration of PCR in the container, the darker the bottle will become. This can often be corrected with colorants but may not be ideal for products needing crystal-clear packaging.
- There’s not enough PCR available to accommodate the growing demand. Although the market is expected to grow as the use of PCR becomes more prevalent.
- You have less control over your product. PCR plastic has already gone through the creation and recycling process, meaning there are elements in the production process (temperature, properties in the materials, etc.) you will not be able to control as closely compared to virgin plastic.
Your company’s commitment to sustainability doesn’t have to mean sacrificing product quality. At ALPS, our testing systems ensure every PCR container and bottle that leaves your line is of the highest durability and integrity. Find out which inspection method is right for your operation.
As part of the TASI Test and Automation’s Packaging Integrity family of businesses, ALPS Inspection is connected with CASSEL Inspection. This relationship with CASSEL Inspection means the ALPS team can offer guidance and technologies to help you develop a comprehensive inspection solution with leak testing and metal detection.
Why Leak Testing is Critical to Protect Your Inventory
Any mass-produced container has the potential to have defects that can lead to leaks. This risk only increases when using containers made with PCR content, making leak testing even more critical.
Investing in leak testing equipment is one of the smartest financial decisions you can make as a blow molding manufacturer. Container inventory can be very high. If the containers holding your product are defective, you may be forced to destroy not only the defective containers but the product itself, resulting in the loss of thousands of dollars.
Leak testing is the only guaranteed way to get the quality assurance you need to keep up with sustainable packaging trends.
If you are a user of PCR plastic, it’s critical your containers and bottles remain high-quality and reliable for the brands you represent. Not only can a leak testing machine detect a defective PCR container or bottle, it can help troubleshoot any issues in your production line that may be causing the defect.
How Does PCR Container Leak Testing Work?
Our versatile leak testing machines have the capabilities to test PCR containers just as you would a container made from virgin plastic, making the transition into sustainable packaging seamless and minimizing any window for defective PCR containers leaving your facility.
Explore our leak testing systems now.
No matter what type of empty, rigid container, ALPS Inspection can help you protect your inventory and your brand image with our reliable, industry-leading leak testing equipment.
In other words, ALPS machines are designed to alarm you to check something in the manufacturing line process — potentially bad material — before you make thousands of poor-quality PCR containers or bottles. Or worse, unknowingly send flawed and defective containers to your customer.