Choked Necks
“Choked neck” defects occur when there is a restriction within the neck of the container, resulting in a pinched neck. The biggest issue with a choked neck defect is that it obstructs the bore and doesn’t allow the filling tube to be inserted, often causing damage to the filling spout and making it impossible for the plastic container to be properly filled.
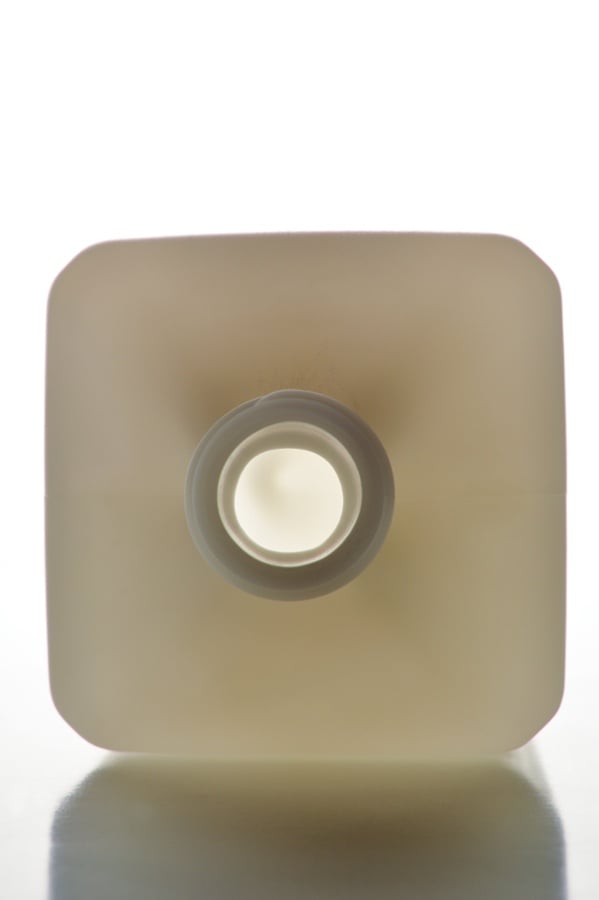
Plastic Material Types at Risk of Choked Neck Defects
Choked neck defects typically occur with High Density Polyethylene (HDPE) in the Extrusion Blow Molding Process (EBM), but can happen with Polyethylene Terephthalate (PET).
Common Causes of a Choked Neck
The following issues can cause a choked neck defect in the blow molding process:
- Problem or issue with the blow pin
- Preform is improperly inserted into the cavity
- Improper parison temperature, which can cause the parison to move, collapse or wrinkle when the mold closes
- Heating is not right on the preform
General Troubleshooting
A choke neck defect is not often easily detected, making it necessary to use a fixed or sensing choke neck probe to inspect inside the neck of the container. If a choked neck defect is present, a fixed probe will not go all the way into the container to seal on the top of the finish. A sensing probe will compress a spring that will trigger a switch indicating a choked neck.
If a choked neck defect is present, the first step in troubleshooting is to ensure the mold setup and operation and the blow pin are correct, or the proper heating and insertion of the preform in the blow mold.
The ALPS Inspection BottleStop Multi-Head Leak Tester is the ideal solution for blow molding manufacturers of angle neck, large, and choked-neck prone containers. Learn more.