BottleStop™ Multi-Head Leak Tester
The ALPS Inspection BottleStop™ Leak Tester delivers unmatched adaptability, efficiency, and reliability. It’s the ideal solution for blow molding manufacturers with angle neck, choked neck-prone, and large containers looking for a cost-effective defect or leak inspection machine.
It provides a superior quality control solution for HDPE containers produced through the Extrusion Blow Molding (EBM) process including everyday household products such as toilet bowl cleaners.
Designed to seamlessly integrate with your existing conveyor system, it ensures consistent quality control at speeds of up to 65 CPM (containers per minute).
How The ALPS BottleStop System Works
BottleStop is designed with flexible configurations, offering two, three, or four test stations (multiple heads) to accommodate various speed and sensitivity requirements. They are also available in three test station types: group or individual handling and hold tooling (with hold tooling required for angle neck containers or applications where we want to detect choked necks).
Containers are fed through the machine by the customer’s conveyor or an optional integrated conveyor system. A gate cylinder regulates the flow of containers at the infeed where programmable sensors monitor their movement through the gate, test station, and reject zones. Rugged, adjustable stroke stop cylinders are used for stable handling, with optional hold tooling for less stable containers.
An integrated cylinder or optional air jet automatically rejects defective containers from the conveyor. The test heads can be set perpendicular or set to match the angle of the container neck to accommodate angle neck and standard containers.
BottleStop is a 100% in-line, automatic, and cost-effective machine, designed to meet the needs of blow molding manufacturers working with angle neck containers in the household, industrial, and automotive industries.
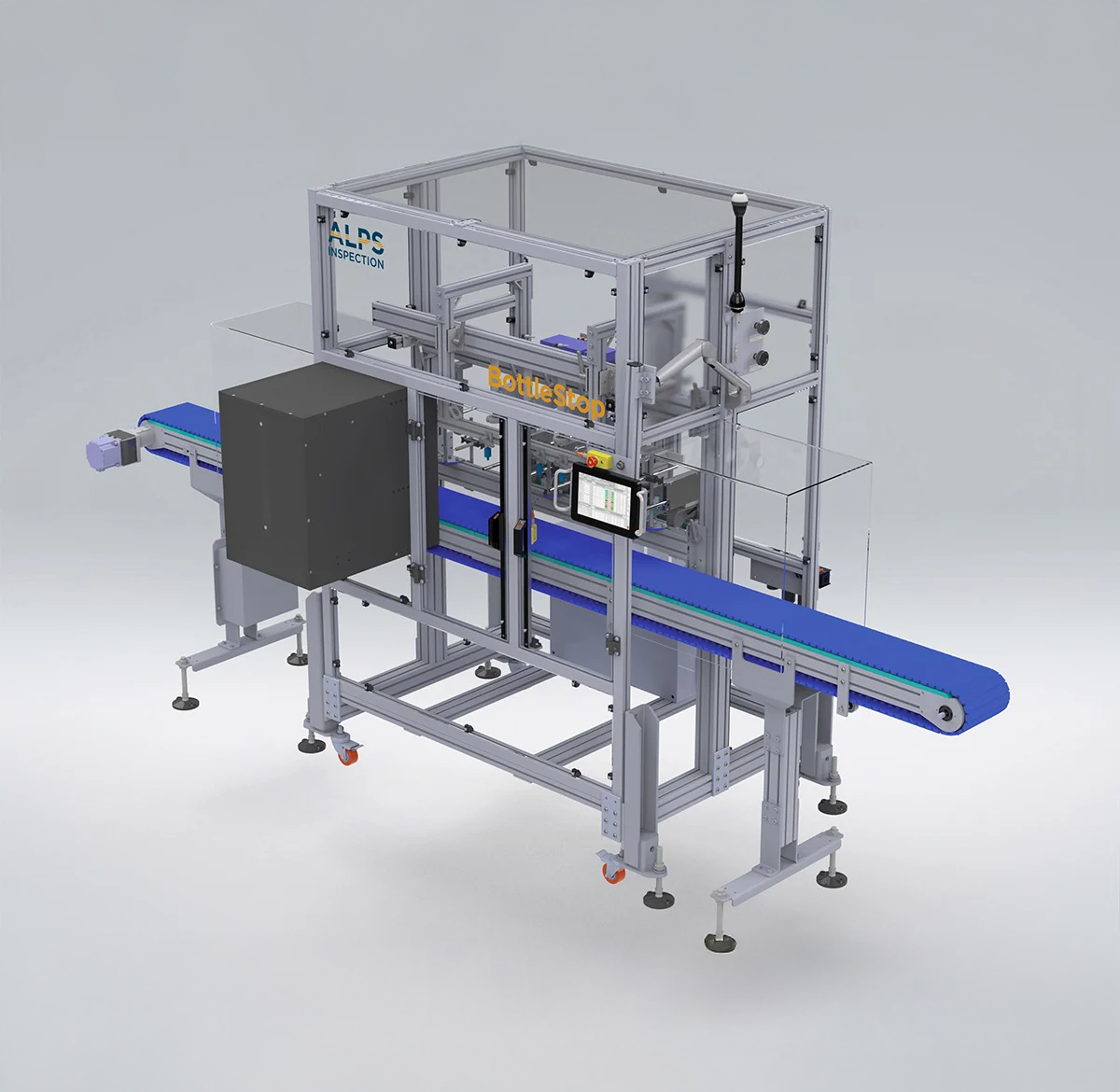
BottleStop Leak Tester
BottleStop provides a streamlined solution for angle neck, choke neck-prone, and large, stable containers produced at speeds up to 65 CPM. It ensures accurate defect inspection with three test modes available: group, individual, and hold tooling, offering maximum accuracy and adaptability.
Features and Benefits
BottleStop offers a range of features and benefits, including:
- Small footprint — Mounts over line conveyor, no line modification or transfers required.
- Testing probe adaptability — The ability to switch between angle neck and standard neck applications makes it versatile for different container types. A choked neck probe is also available.
- Automated testing performance — Gate cylinder regulates containers into the testing area. Precise, programmable sensors are used to monitor container travel through the gate, test station, and reject areas.
- User-friendly, intuitive controls — Full-color HMI touchscreen operation with numerous features, including data graphs and reports, enabling efficient process tracking and continuous improvement.
- High-speed efficiency — Capable of inspecting up to 65 containers per minute (depending on container size), ranging from 1” to 13” in diameter/length.
- Integrated self-test function — Verify the detection of a defined hole size with push-button control, ensuring the system is properly set up to detect the appropriate hole size. It can also be automated for added convenience.
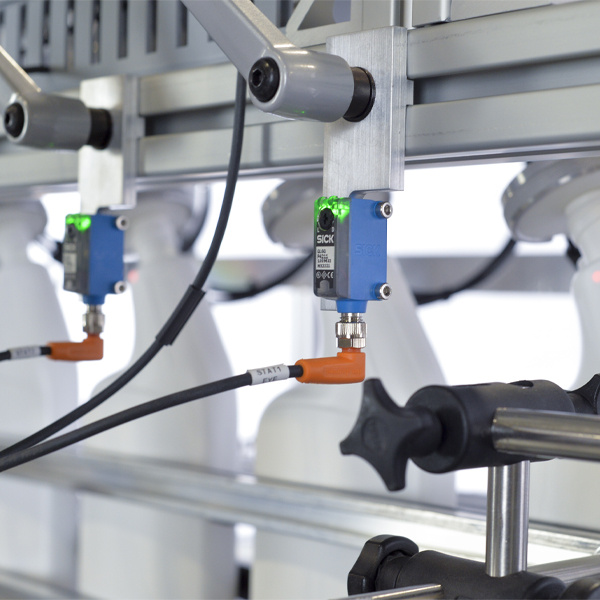
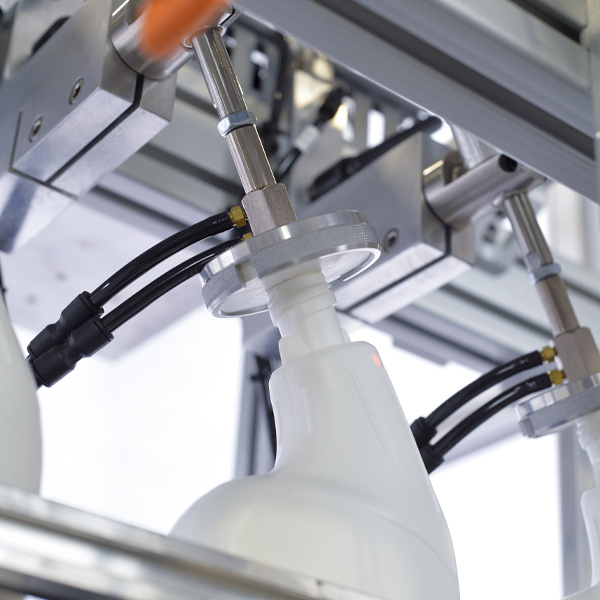
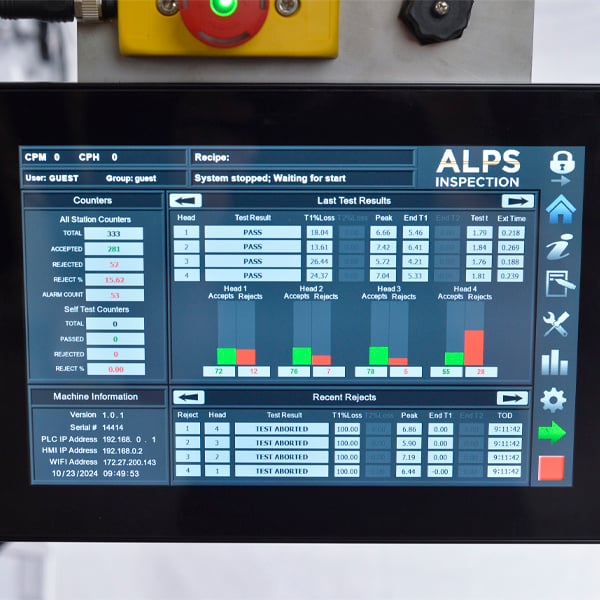
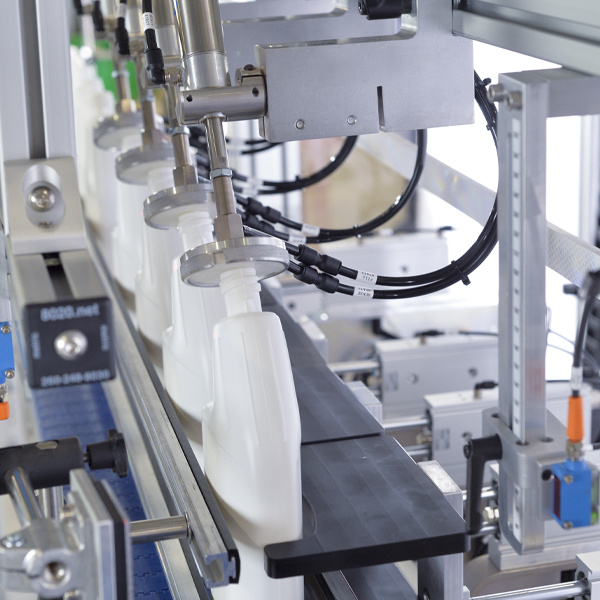