Finish Trim Defects and Trim Defects
After some blow molding processes, a piece of plastic is still attached to the bottom and/or top of the container, which is then sliced off by a rotary cutter blade or punch trimmer. A "finish trim defect" occurs when the blade or trimmer cannot properly remove the excess plastic at the top of the container or leaves little cuts or "hangnails" in the sealing surface of the container.
The trimmer may also cause a hole when removing the tail at the bottom of the container, which is also a type of trim defect.
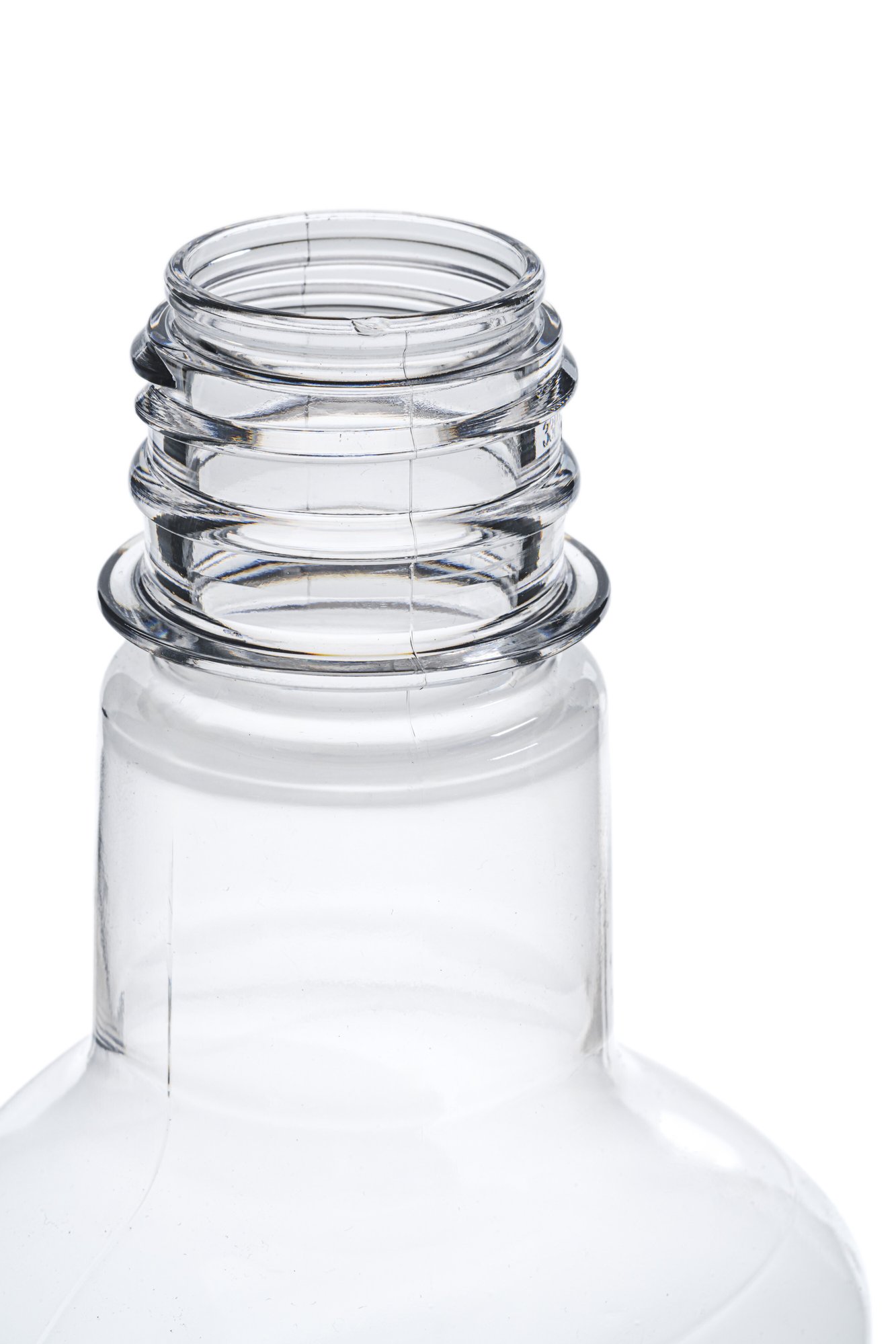
Plastic Material Types at Risk of Finish Trim Defects
Trimming defects are most often associated with High Density Polyethylene (HDPE) in the Extrusion Blow Molding (EBM) process, as every EBM bottle must be trimmed. Occasionally, wide mouth Polyethylene Terephthalate (PET) plastic bottles in the Stretch Blow Molding Process (RSBM) are blown from a standard preform and then trimmed.
Common Causes of Finish Trim Defects
Finish trim defects are commonly caused by problems with the blade or trimmer, such as dullness or incorrect setup.
General Troubleshooting
All ALPS leak testers have a range of seal durometers that control the probe pressure to make the finish trim defects appear as a leak. If a finish trim defect is detected, evaluate your blow molding process and ensure your blade or trimmer is aligned correctly.