Short Shot Defects
A short shot defect occurs when the volume of plastic needed to fill the mold cavity is short by some amount. Because the plastic is injected from the bottom of the preform, the missing material is seen at the top of the preform, where the sealing surface is. In other words, the molten plastic injection is short and leaves the container incomplete and deficient, hence the name “short shot.”
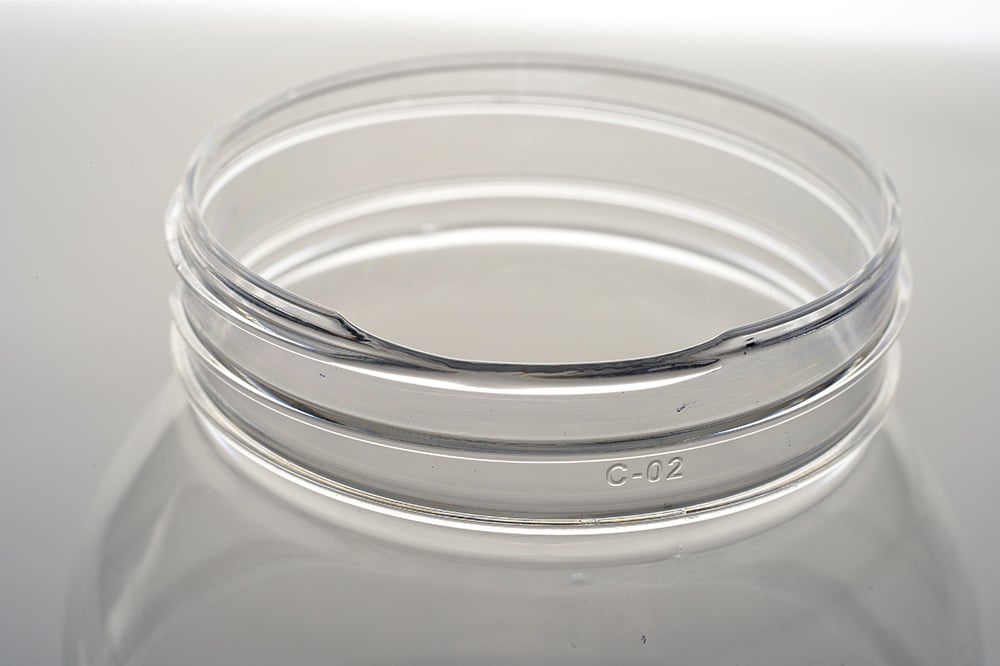
Plastic Material Types at Risk of Short Shots
Short shot defects are most common in High Density Polyethylene (HDPE) and Polyethylene Terephthalate (PET) plastic materials during blow molding processes where the injection step forms the finish in the preform, including Injection Blow Molding (IBM), One-Step Stretch Blow-Molding (ISBM), or Two-Step High-Speed Stretch Blow Molding (RSBM).
Common Causes of Short Shots
There are several reasons why a short shot defect may occur, including:
- Flow restriction due to narrow or blocked gates within the mold
- Molten plastic is too viscous and may solidify before reaching all cavities
- The mold is too cold to allow the molten plastic to completely fill the cavity before cooling
- Inadequate venting technique resulting in air or gas pockets
- Inadequate injection pressure
General Troubleshooting
If a short shot is detected, adjust your injection blow molding machine and examine your blow molding process, which may include increasing injection speed, pressure, and temperature or redesigning your mold with wider channels and gates. Some short shots can be detected on ALPS leak testers by using tilted probes with harder seal durometers.